Materials of the highest quality
Materials in use within SBR° parts are of the highest quality rubber and silicone.
We produce a wide range of components for machinery and applications across key areas of industry and manufacturing. These include parts for use in commercial/military aircraft and helicopters through to showers and audio equipment.
We use British Standard and Department of Technical Development (DTD) for our military customers and specification materials from approved suppliers. These have been fully tested and released with certificates of conformance and testing. All manufactured parts are fully batch traceable and documented.
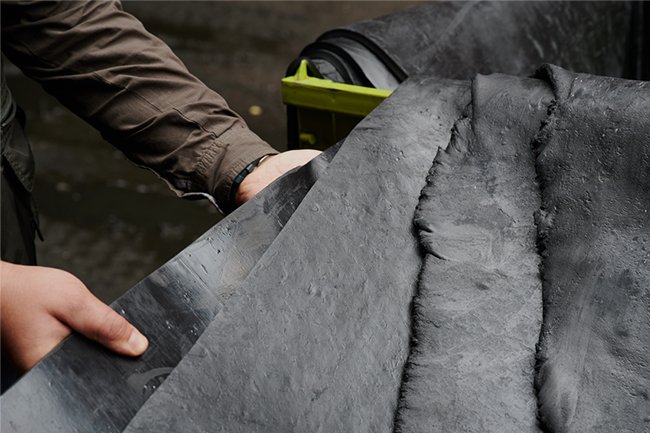
From punching gaskets and seals to compression moulded O-rings and bellows, our material options are comprehensive.
Our full range of materials
Click to read more
XClose
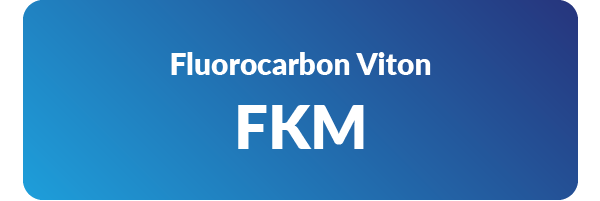
FKM is a fluoroelastomer which is also commonly referred to as Viton™, FKM or FPM. FKMs offer excellent resistance to extreme temperatures and harsh chemicals such as oils, fuels and greases.Good temperature properties Excellent oil resistance Excellent ozone and sunlight resistance Poor steam resistance
Hardness Range: 50 – 95 IRHD
Operating Temperature: -25°C to +200°C
Typical Use
FKM products can typically be found within fuel, oil and chemical processing systems.
Advantages
Disadvantages
Please call +44 (0)23 9225 5180 to discuss your enquiry, get in touch by emailing sales@sbr.aero or complete our online contact form.
Click to read more
XClose
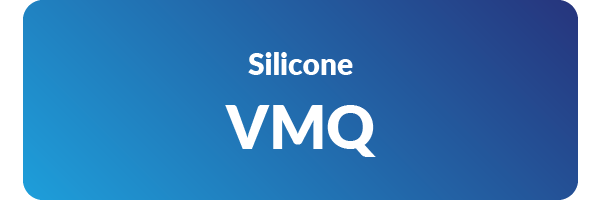
Silicone elastomers hold a greater temperature range, making them perfect to use across both high and low temperature environments. Silicone elastomers also hold superior resistance to UV radiation, ozone and dielectric properties.
Hardness Range: 20 – 90 IRHD
Operating Temperature: -60°C to +230°C
Typical Use
Silicone products can typically be found within jet engines, electrical insulative and conductive applications and medical devices due to its bio-compatibility and durability.
Advantages
- Excellent high and low temperature properties
- Excellent ozone and sunlight resistance
Disadvantages
- Tear strength
Please call +44 (0)23 9225 5180 to discuss your enquiry, get in touch by emailing sales@sbr.aero or complete our online contact form.
Click to read more
XClose
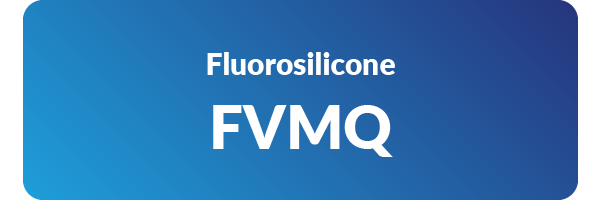
Fluorosilicone is an incredibly durable material with enhanced resistance to chemicals, fuels, oils and lubricants. FMVQ also has a wide temperature range as well as superior ability to counteract the effects of weathering and ozone exposure.
Hardness Range: 30 – 90 IRHD
Operating Temperature: -60°C to +190°C
Typical Use
Silicone products can typically be found within jet engines, electrical insulative and conductive applications and medical devices due to its bio-compatibility and durability.
Advantages
- Good high and low temperature properties
- Excellent ozone and sunlight resistance
- Excellent oil resistance
Disadvantages
- Tear strength
- Gas permeability
Please call +44 (0)23 9225 5180 to discuss your enquiry, get in touch by emailing sales@sbr.aero or complete our online contact form.
Click to read more
XClose
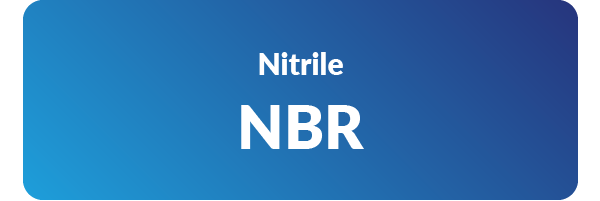
Nitrile is also commonly known as Buna-N and acrylonitrile butadiene rubber. NBR is known for its excellent resistance against fuels, oils and grease as well as abrasion and tear resistance and is often one of the first choice materials within aerospace and oil industries.
Hardness Range: 40 – 95 IRHD
Operating Temperature: -30°C to +125°C
Typical Use
Nitrile products are typically the economical choice for users requiring high resistance to fuel, grease and oils and can be commonly found within fuel systems.
Advantages
- Excellent fuel, grease and oil resistance
- Strong acid resistance
- Strong abrasion resistance
Disadvantages
- Poor ozone and sunlight resistance
- Poor gas permeability
Please call +44 (0)23 9225 5180 to discuss your enquiry, get in touch by emailing sales@sbr.aero or complete our online contact form.
Click to read more
XClose
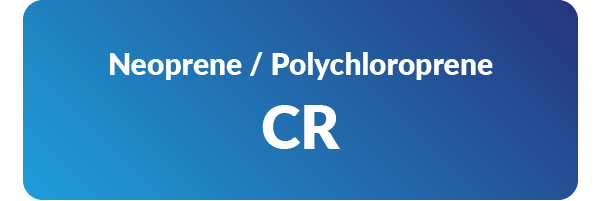
Polychloroprene is also commonly known as Neoprene. NBR is known for its excellent resistance against fuels, oils and grease as well as abrasion and tear resistance and is often one of the first choice materials within aerospace and oil industries.
Hardness Range: 40 – 90 IRHD
Operating Temperature: -30°C to +100°C
Typical Use
Neoprene is a versatile compound often used within fire protection accessories and also within the marine industry due to its durability and resistance to weathering.
Advantages
- Excellent ozone resistance
- Good oil resistance
- Strong tear and abrasion resistance
Disadvantages
- Poor compression set resistance
- Poor fuel resistance
Please call +44 (0)23 9225 5180 to discuss your enquiry, get in touch by emailing sales@sbr.aero or complete our online contact form.
Click to read more
XClose
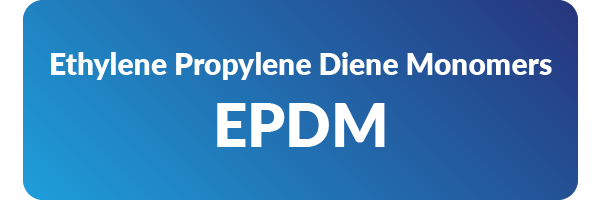
EPDM is one of the most commonly used materials in the elastomer industry. Ideal for applications which require strong ozone and general weathering resistance as well as those in harsh chemical environments, EPDM has continued to hold a reputation for being one of the most cost-effective material options.
Hardness Range: 40 – 95 IRHD
Operating Temperature: -50°C to +150°C
Typical Use
EPDM is typically utilised in a variety of applications and product types including O-rings, gaskets and hoses. EPDM products can be found across multiple industries and as such can be found within ventilation systems and electrical insulating units.
Advantages
- Excellent ozone and sunlight resistance
- Good oil resistance
- Strong tear and abrasion resistance
Disadvantages
- Poor fuel resistance
Please call +44 (0)23 9225 5180 to discuss your enquiry, get in touch by emailing sales@sbr.aero or complete our online contact form.
Click to read more
XClose
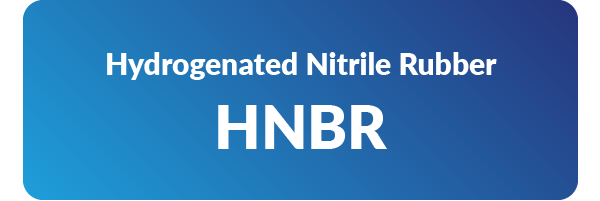
HNBR is a hydrogenated version of Nitrile (NBR) rubber. HNBRs hold greater resistance to oil and chemicals than nitrile rubbers and can also withstand increased temperatures.
Hardness Range: 50 – 95 IRHD
Operating Temperature: -25°C to +150°C
Typical Use
HNBR is widely used across industries and is often utilised within both dynamic and static applications within oil and chemical systems. Common HNBR products include O-rings, seals and hoses.
Advantages
- Good ozone and sunlight resistance
- Strong oil resistance
- Strong abrasion resistance
Disadvantages
- Decreased low temp resistance in comparison to standard nitrile
Please call +44 (0)23 9225 5180 to discuss your enquiry, get in touch by emailing sales@sbr.aero or complete our online contact form.
Click to read more
XClose
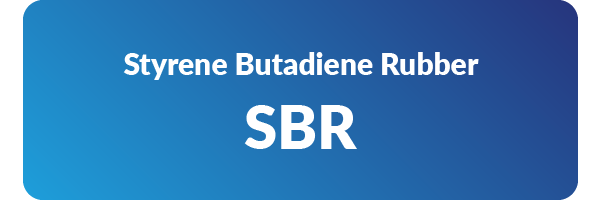
Styrene Butadiene Rubber (SBR) is a synthetic rubber known for its abrasion, high tensile strength, resistance and low cost. Because of this, SBR is a staple material within automotive and industrial sectors due to this point.
Hardness Range: 40 – 95 IRHD
Operating Temperature: -25°C to +90°C
Typical Use
SBR products can be commonly found within the automotive and industrial applications and, thanks to its adhesion and abrasion resistance, is also used to form gaskets as well as basic moulded products.
Advantages
- Excellent abrasion and tensile strength
- Strong water resistance
- Low cost
Disadvantages
- Poor oil resistance
- Poor ozone and sunlight resistance
Please call +44 (0)23 9225 5180 to discuss your enquiry, get in touch by emailing sales@sbr.aero or complete our online contact form.
Click to read more
XClose
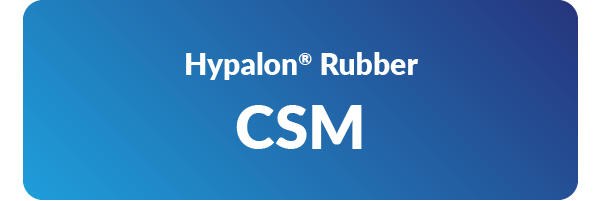
Hypalon, also known as CSM, is a chlorosulfonated polyethylene synthetic rubber and is noted for its resistance to chemicals, temperatures and UV.
Hardness Range: 40 – 95 IRHD
Operating Temperature: -40°C to +140°C
Typical Use
Due to its resistance to chemicals, temperatures and UV, CSM is commonly used for seals and equipment protection throughout multiple applications including defence and automotive.
Advantages
- Excellent ozone and sunlight resistance
- Strong tear and abrasion resistance
- Good acid and oil resistance
Disadvantages
- Poor fuel resistance
- Low temperature properties
Please call +44 (0)23 9225 5180 to discuss your enquiry, get in touch by emailing sales@sbr.aero or complete our online contact form.
Click to read more
XClose
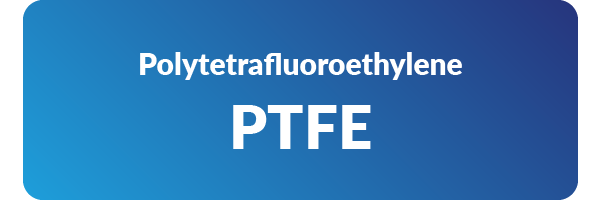
Polytetrafluoroethylene (PTFE) is a non-flammable synthetic resin produced by the polymerisation of tetrafluoroethylene and is widely used across all industries.
Hardness Range: 70 – 85 IRHD
Operating Temperature: -30°C to +200°C
Typical Use
PTFE is more often the choice for gaskets, washers and seals due to its corrosion resistance and chemically inert properties. PTFE is a staple material across all industries including aerospace and defence.
Advantages
- Excellent chemical resistance
- Excellent ozone and sunlight resistance
- Cost effective
Disadvantages
- Higher sealing force required in comparison to standard elastomer seals
Please call +44 (0)23 9225 5180 to discuss your enquiry, get in touch by emailing sales@sbr.aero or complete our online contact form.
Click to read more
XClose
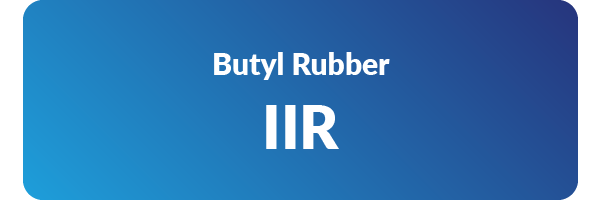
Butyl Rubber, also called isobutylene-isoprene rubber (IIR) is impermeable to gas, resistant to water, steam and also weathering.
Hardness Range: 40 – 90 IRHD
Operating Temperature: -40°C to +120°C
Typical Use
Butyl Rubber's very low resilience makes it suitable for shock, damping and anti-vibration products. Common products include O-rings, seals and anti-vibration products.
Advantages
- Excellent water resistance
- Good resistance to acids
Disadvantages
- Poor oil resistance
Please call +44 (0)23 9225 5180 to discuss your enquiry, get in touch by emailing sales@sbr.aero or complete our online contact form.
Click to read more
XClose
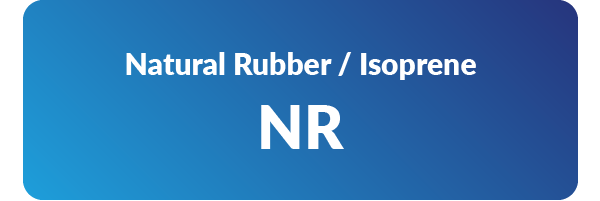
Natural Rubber is made up of long isoprene polymer chains, loosely connected. As opposed to synthetic rubbers, which are produced from petrochemicals, natural rubber is derived from latex sap of rubber trees.
Hardness Range: 30 – 90 IRHD
Operating Temperature: -45°C to +75°C
Typical Use
Natural Rubber can be commonly found within the industrial industry. Products include seals, gaskets and anti-vibration solutions.
Advantages
- Excellent tear strength
- Strong compression set
Disadvantages
- Poor oil resistance
- Poor UV resistance
Please call +44 (0)23 9225 5180 to discuss your enquiry, get in touch by emailing sales@sbr.aero or complete our online contact form.
Click to read more
XClose
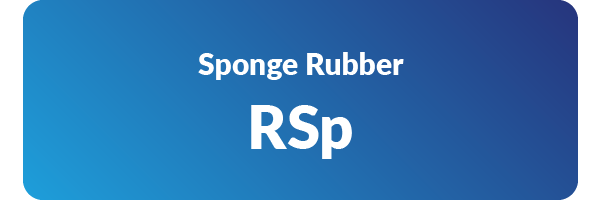
Open-cell and closed-cell sponge rubber can be produced in various densities ranging from soft to hard sponge depending on requirement. Sponge rubber is also available in a variety of material types including silicone, neoprene and fluorosilicone.
At Southbourne Rubber we utilise the latest technologies to produce gaskets, seals, washers and custom products from sponge material.
For more information or for further assistance, please call +44 (0)23 9225 5180 to discuss your enquiry, get in touch by emailing sales@sbr.aero or complete our online contact form.
Click to read more
XClose
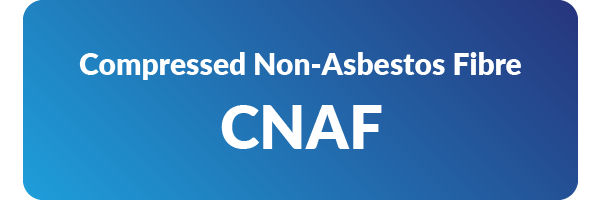
Compressed Non-Asbestos Fibre (CNAF) is a high grade sealing and jointing material. CNAF commonly is produced in sheet form before being converted to products which include gaskets, washers and custom shaped components.
At Southbourne Rubber we utilise the latest technologies to produce gaskets, washers and custom shaped products from CNAF material.
For more information or for further assistance, please call +44 (0)23 9225 5180 to discuss your enquiry, get in touch by emailing sales@sbr.aero or complete our online contact form.
Click to read more
XClose
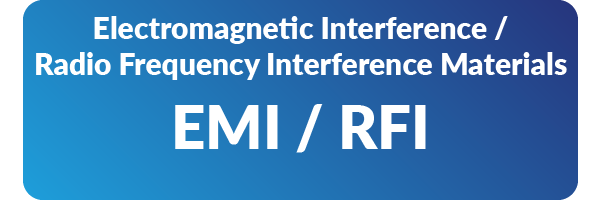
Electromagnetic Interference (EMI) can disrupt the performance of electronic equipment. A common manifestation of EMI is radio frequency (RF) signal loss, which can impact communication systems and connections.
EMI/RFI materials can both be purely elastomer based produced from materials such as silicone and fluorosilicone but can also commonly be found with fillers including copper, metal, graphite, nickel and silver. These materials are produced in sheet form before being converted to produce products which include gaskets, washers and custom shaped components.
At Southbourne Rubber we utilise the latest technologies to produce gaskets, washers, custom shaped products from EMI and RFI materials.
For more information or for further assistance, please call +44 (0)23 9225 5180 to discuss your enquiry, get in touch by emailing sales@sbr.aero or complete our online contact form.
Click to read more
XClose
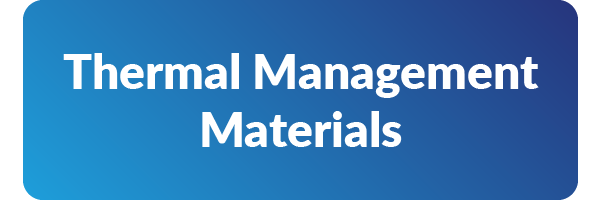
Thermally conductive materials are often designed for use where the highest possible thermal, dielectric and mechanical properties are required. Thermal Management products are often found within power applications including conversion equipment and supplies across multiple industries such as aerospace and defence.
Thermal Management materials are often produced in sheet form or continuous rolls before being converted into products such as pads, gaskets and custom shaped components.
At Southbourne Rubber we utilise the latest technologies to produce these products from thermally conductive and insulating materials.
For more information or for further assistance, please call +44 (0)23 9225 5180 to discuss your enquiry, get in touch by emailing sales@sbr.aero or complete our online contact form.Material properties
It is crucial within the design process, that the correct material is selected and operates against the required characteristics and environment for the end application.
To aid this process, we have an extensive material property chart covering the performance in basic rubber properties.
Click on our downloadable ▼ material properties chart opposite for detailed information.
